
Thermal Conversion
Involves the use of heat, with or without the presence of oxygen, to convert biomass materials into other forms of energy. Basic thermal conversion technologies include direct combustion, pyrolysis, and torrefaction.
Combustion
Direct combustion is the burning of biomass in the presence of oxygen. Boilers and furnaces are typically used to drive turbines to produce electricity or to produce steam to be used in district heating/cooling systems. Biomass burns in a combustion chamber, converting the biomass into heat, in a furnace. In there, the heat is distributed in the form of water or hot air. The heat of combustion is converted into steam in a boiler. The steam can be used to produce mechanical energy, electricity, or heating and cooling. Roughly 60-85% of the energy in biomass fuel could be found in a boiler’s steam.
Co-firing is a practice that permits biomass feedstocks to be used early on in the renewable energy transformation. It is the combustion of a fossil-fuel, like natural gas or coal, with a biomass feedstock. Numerous advantages are associated with co-firing, especially when electricity is an output. It is clear that fossil-fuel power plants are highly polluting in terms of GHSs, CO2 , and sulfur. To co-fire biomass may be a cost-effective way to meet the more stringent emission targets if we utilized exiting equipment with some modifications. The low sulfur content of biomass fuel allows it to potentially offset the higher sulfur content of fossil fuel.
“Biomass can also be used in co-generation, also called combined heat and power (CHP) which is the simultaneous production of heat and electricity. All power plants produce heat as a by-product of electricity production, and this heat is typically released to the environment through cooling towers (which release heat to the atmosphere) or discharge into near-by bodies of water. However, in CHP processes, some of the “waste heat” is recovered for use in district heating. Co-generation coverts about 85% of biomass’ potential energy into useful energy.” (Citation T-28).
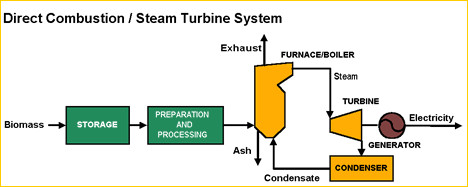
Citation I-98
Pyrolysis and torrefaction do not necessarily produce useful energy directly, but under controlled temperature and oxygen conditions, they are used to convert biomass feedstocks into gas, oil or forms of charcoal. Compared to the original biomass, these energy products are more energy dense. Also, due to their low transport costs, or more predictable and convenient combustion characteristics, they are able to be used in internal combustion engines and gas turbines.
Pyrolysis is a process of subjecting a biomass feedstock to high temperatures (greater than 430 °C) at low oxygen levels and under pressurized environment. In the process, biomass undergoes partial combustion. Processes of pyrolysis result in liquid fuels and a solid residue called char, or biochar. Biochar is like charcoal and rich in carbon. Liquid phase products result from temperatures which are too low to destroy all of the carbon molecules in the biomass so the result is production of tars, oils, methanol, acetone, etc.
Torrefaction, similar to pyrolysis, is the conversion of biomass with the application of heat in the absence of oxygen, but at lower temperatures than those typically used in pyrolysis. In torrefaction, temperatures typically range between 200-320 °C. Water is removed and cellulose?, hemicellulose and lignins are partially decomposed in the torrefaction process. The final product is an energy dense solid fuel frequently referred to as “bio-coal”.
Pyrolysis and Torrefaction
Pyrolysis Process
Citation V-3